Introduction:
Superheat began in 2000, at a time when the industry was still using outdated procedures and equipment that exposed the workforce to unnecessary safety risks. Superheat was founded on the principal that innovation and technology advancements can produce a safer, more cost-effective and quality driven way to provide on-site heat treatment services.
“Advancing Heat Treatment™” isn’t simply a catchy tagline. We understand heat treatment specifications are consistently changing and safety requirements have become increasingly demanding. Therefore, we continually forecast the need for more sophisticated devices and equipment to provide a safer overall heat treatment process. Through technology advancements we have minimized the human footprint of essential staff on the job site, decreasing the overall exposure risk and taken a data analytic approach that puts safety at the forefront of our operations.
Equipment:

Superheat prides itself on remaining ahead of the innovation curve while maintaining a diligent effort to stay up to date with the latest industry news and information pertaining to industrial on-site heat treatment. At Superheat, we are the only company in the world dedicated to the true remote operation of on-site equipment from our centralized off-site Superheat SmartCenter™. Through a patented process that integrates remote operation technology and equipment advancements we provide an on-site heat treatment service in which 100% of the equipment and therefore heat cycles are controlled remotely. When compared to the industry standard, Superheat reduces the required man hour footprint on job sites by up to 40%, thus decreasing the headcount through clients’ gates and ultimately removing field staff from potential hazardous areas.
Continual investment in research and development coupled with our in-house manufacturing division ensures we have complete control over the safety features built into our equipment and process. As noted above, our Superheat SmartPoint™ and Superheat SmartGen™ heat treatment consoles are engineered to be remotely operated, thus can be shut down or power can be initiated in any environment. Therefore, in the event of emergencies our field personnel are only concerned with their wellbeing and the safe exit of the facility, wasting no unnecessary time powering down equipment. Our heat treatment consoles are also commercial grade dedicated compliant with CLASS 1 Nuclear Programs and the only heat treatment consoles approved to UL# 508A/CSA #C22 No.14-10. The highest of safe manufacturing practices and circuitry standards.

Lastly, our Superheat SmartPak™ is the only piece of equipment in the industry to provide safety lock out capability directly at the component location to minimize the risk of electric shock to field personnel. Upon the completion of standardized training each technician receives a personalized Superheat SmartCard™ which utilizes nearfield technology when swiped at the Superheat SmartPak™ to lock out power to designated components immediately at the work location. Putting the control over safety directly at the individual level and removing the need for staff to leave the work area to isolate power of the entire equipment consoles which can be far distances away from the component being heat treated. The swipe of this card to the Superheat SmartPak™ also indicates to our panel operator they can safely start the heating process and the weld area is in a safe condition to proceed.

We have integrated some of the most accredited industrial energy producers into the ground-breaking Superheat SmartView™ Interactive Web Based Quality Assurance & Project Management Platform that includes everything from client requests to final QA package downloads. This web-based portal grants approved client staff the opportunity to digitally upload requests, view live heat treatment charts, and weld statuses remotely. The web-based platform integrates download capabilities to retrieve QA Superheat SmartReport™ packages eliminating the need for QA representatives to physically be on site or exchange printed documentation.
Metrics:
Superheat SmartView™ is also a digital safety hub for internal staff, providing them instant access to all safety procedures and an area to exchange safety data for analysis. From the SmartView employee portal project managers can obtain site specific safety protocols, access lessons learned, review PPE requirements related to their scope, manage PAR (personal accountability rosters) per job site and even review approved drivers lists. This interactive platform gives site management the tools and knowledge necessary to create a safe working environment for their field team members. Additionally, the document upload feature in SmartView enables site level managers to share daily tailgates, submit safety near misses and incidents, and exchange other pieces of critical information pertaining to our safety programs. This data is then audited at the regional and even national level during KPI meetings. Should negative or positive trends be found corrective actions and/or improvements can be built into procedures. This proactive approach to collection, distribution, and analysis of safety data is made possible through digital innovation. The result is a profound effect on our ability to maintain the highest industry safety standard in relation to key metrics such as EMR, TRIR, LTI.
Recognition & Safety Involvement:
It is Superheat’s intent for employees to be actively involved and recognized in the safety process. To accomplish this, Superheat has adopted the process termed “Safe Work Action Team” or “SWAT”. This process promotes the ongoing involvement of employees through observations of their peer’s while they are performing work. Immediate feedback is given to the observed employee regarding behaviors, both positive and negative. Observation data is documented and shared with employees during safety meetings and postings. Employee teams have monthly meetings to discuss their activities, trends, ideas, and recommendations to improve the safety process and address trends.
The primary objectives of the SWAT are:
- Excel in safety – be the best
- Recognize and reinforce safe behaviors
- Have the ability to recognize and eliminate “At Risk” behaviors with immediate intervention
- Create a safety culture focused on improving behaviors prior to an incident or accident
- Utilize the SWAT data to develop injury prevention initiatives and reward successes
- Incorporate trust among coworkers to keep watch on one another without question or reprimand
- Promote ownership of the process and active employee involvement
Field Technicians at all levels are encouraged to promote the identification of at-risk behaviors so that they can be eliminated from the work areas through feedback and intervention. Field staff use SWAT cards to document workplace recommendations and actions to the Superheat Safety Department and Management. SWAT cards are then logged and the number of submissions per individual per month is tracked. Recognition of participants is as follows:
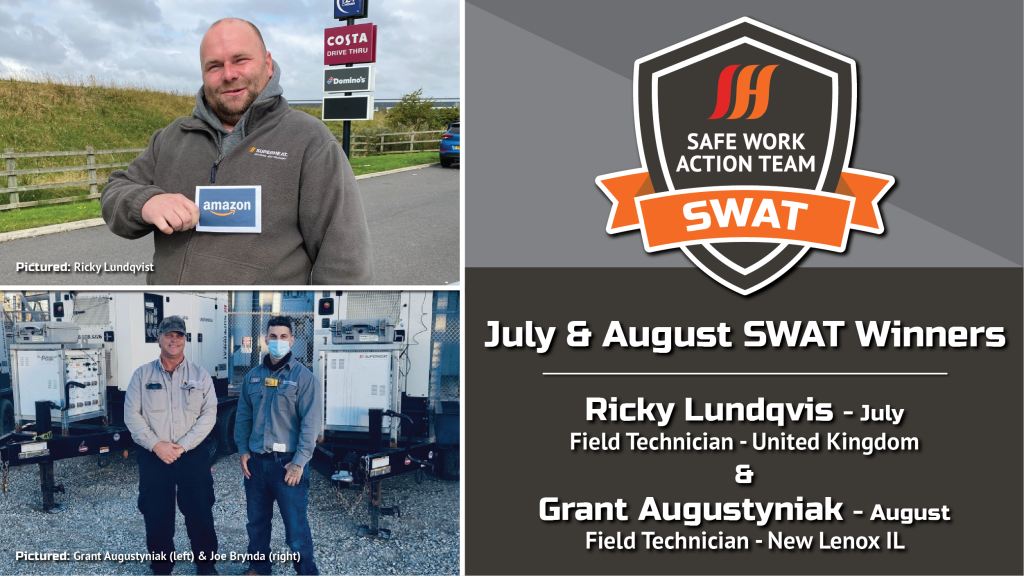
Level 3 – Participant
All participants who submit valid SWAT cards each month will be recognized in an appreciation email to their Regional Manager from the Safety department and be eligible for selection for an award.
Level 2 – Silver User
Participants who submit 4 valid SWAT cards in a month will be recognized in the internal SuperNews publication.
Level 1 – Smart User
All participants who submit 5 or more valid SWAT cards in a month will be recognized on the Superheat social media platforms (Facebook, Linked-In Twitter) and will be recognized in the internal SuperNews publication.
Monthly winners are then added to a pool. Two quarterly winners are then chosen by SWAT members. Awards are then chosen by the winners and can be utilized to impact their family such as gift cards. The eight quarterly winners are then eligible for the annual award chosen by SWAT members. Annual award will have $500 maximum value. All winners will be recognized via company safety newsletter and selected social media platforms.
Conclusion:
Through our equipment innovations, Superheat SmartView QA Digital Platform, and safe work recognition programs and practices our claims that Superheat is the safest on-site heat treatment service provider in the industry are reflected through our safety metrics (see below). We are proud to report having zero recordable injuries from 2019-2021 with a goal to continue this in the coming years. At Superheat, we hold safety in highest regard and are constantly striving to go above and beyond in improving our safety initiatives.
